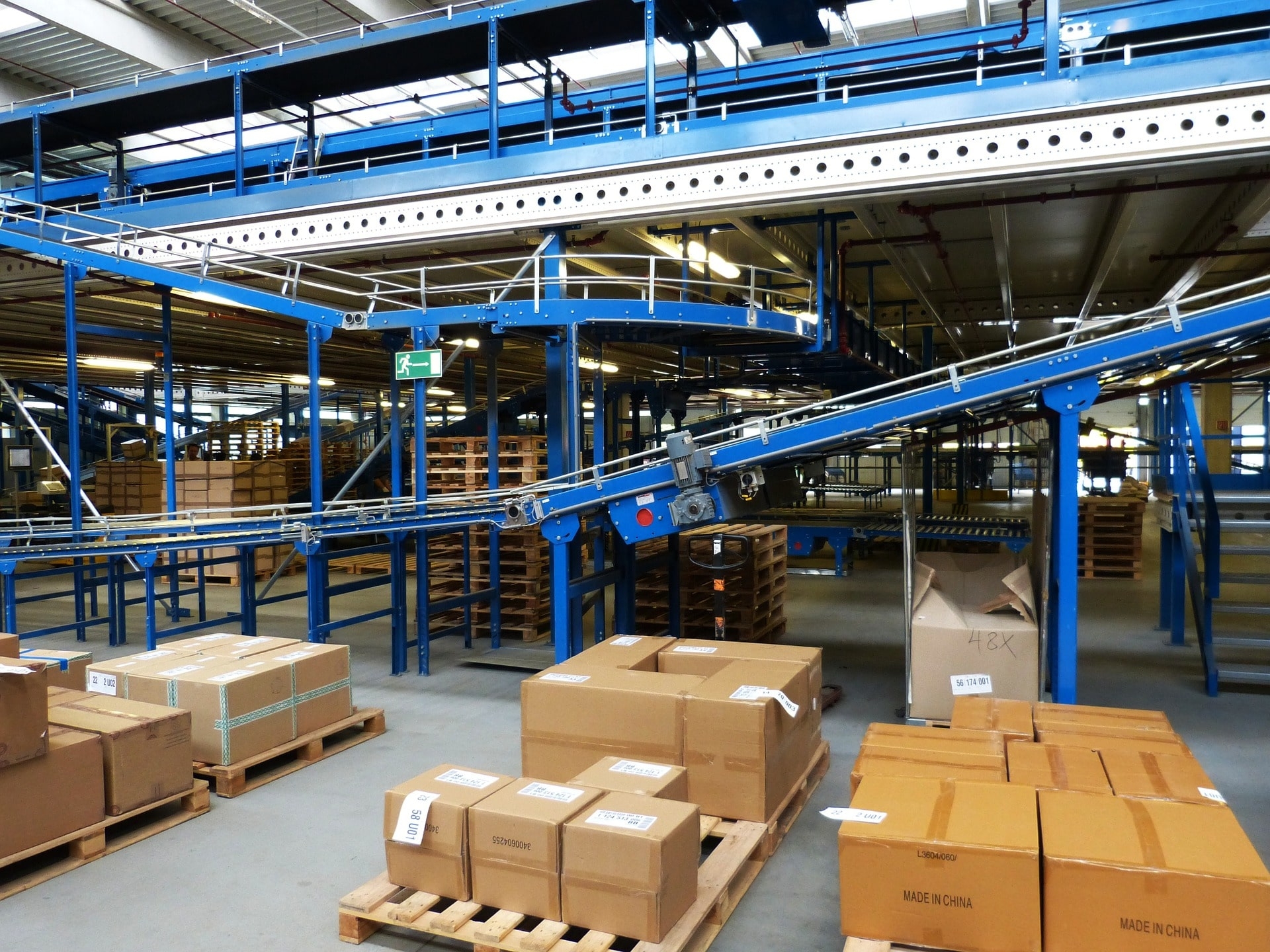
Warehouse Automation Projects
Warehouse Automation
What does the term “warehouse automation” mean to you? It can have a lot of meanings, but at the big picture level it means using machines to do at least some of the work involved in moving goods where they need to go. In this post, we’ll try to clearly explain how Pendant fits into the broad scope of warehouse automation.
Typically, Pendant receives orders for warehouse automation projects from conveyor handling systems integrators. The conveyor experts design an automated system for receiving, moving, sorting, packaging, and shipping all kinds of goods. These systems may include many different types of conveyors, scanners, sorters, labeling and packaging machines, scales, and robots. Pendant’s job is to get it all to work together efficiently to maximize the clients’ return on investment by designing the control system.
Here is how the project usually flows.
- A systems integrator issues a request for a quote (RFQ) to Pendant.
- Pendant estimates the cost to complete the system including startup and commissioning.
- Pendant prepares a quote with a fixed investment for the systems integrator.
- The systems integrator issues a purchase order and the warehouse automation project begins.
- Pendant’s design engineers create coordination and control panel drawings using AutoCAD Electrical.
- The design engineer creates a bill of materials to be used to order materials for the panels that need to be built.
- A Pendant Controls Engineer starts the process of programming the PLC.
- Pendant’s Panel Shop swings into action and begins to build the control panels and assemble the field devices and spare parts for shipment to the end user.
- The programmer continues to write the PLC program using ladder logic. Pendant’s goal is to have the program as close to complete as possible before we arrive at the client’s site for startup and commissioning.
- The programming team develops the HMI screens and middleware/WCS that allows for communication between the control system and the client’s ERP or Warehouse Management System software.
- The Panel Shop completes the panels and turns them over to the programmer for testing.
- The panel shop team ships the completed panels, field devices, and spare parts to the client site.
- The design team updates the CAD drawings.
- The startup techs head for the client site to participate in the correct installation of the control system panels and devices, testing the input/output loops, testing the conveyor system in operation, and ultimately commissioning the system and turning it over to the client.
In simpler terms, these are the warehouse automation project phases in which Pendant is involved:
- Preparing the quote
- Design
- Panel build
- Programming/Software
- Startup, commissioning, and go-live support
- Post-project support
Now that you understand the range of Pendant’s activities, let’s see if we’re a fit. You can start at the first bullet point above…