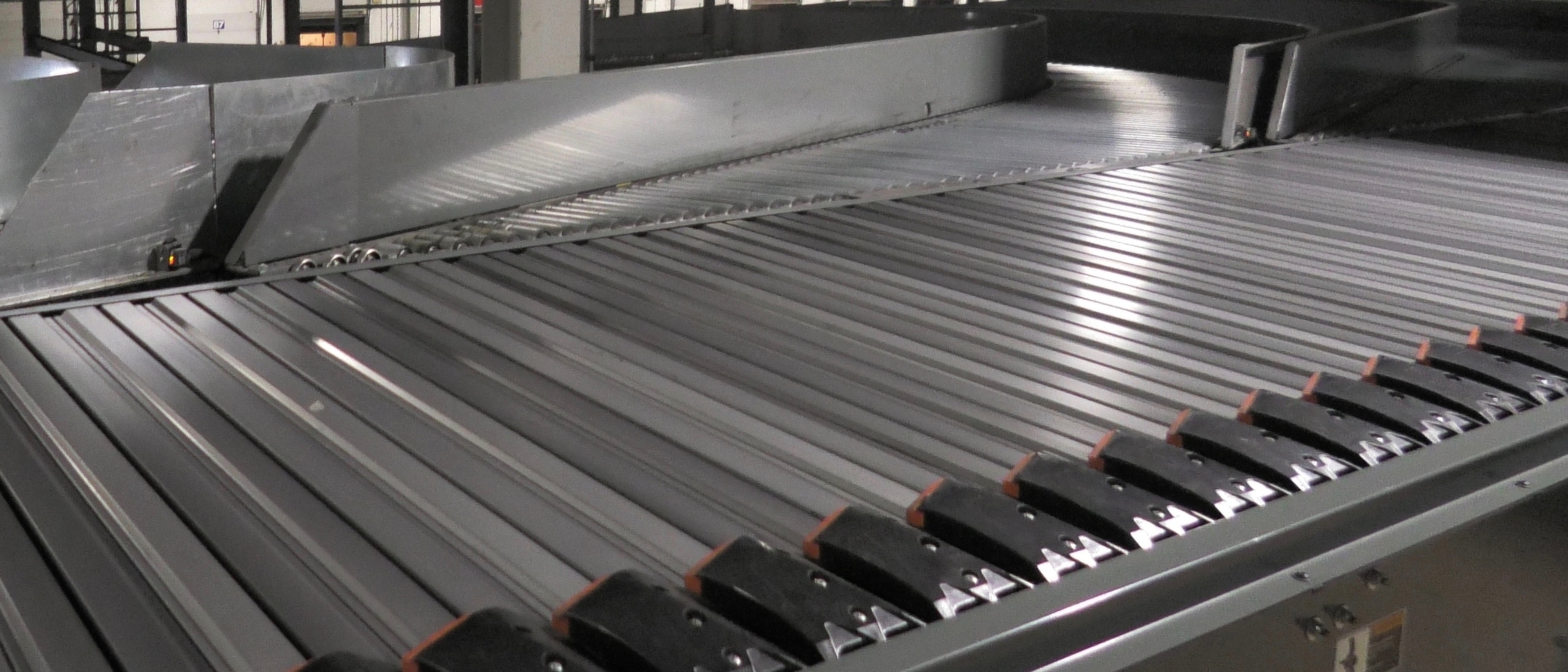
Conveyor Merges and Sortation
Rob, James, and I visited a local retail client this week to take a look at their existing slide shoe sorter in operation. The system includes a 7:1 sawtooth conveyor merge and a large scan station upstream of the sorter.
This particular sorter operates at speeds as high as 550 feet per minute. Most of the packages come in at the receiving end of the warehouse and go to the sorter for immediate dispatch to the retail stores the warehouse serves. Some packages go to inventory in the warehouse.
To meet the production goals, the conveyor merge, scanner, and sorter must operate with precision and reliability. The system design is critical, but the PLC programmer plays a key role.
Some Numbers
Let’s take a look at some numbers. Assume that the average package occupies 12″ of conveyor space. Assume also that the designed gap between packages is 12″. Including the gap, each package takes up 2 feet. The maximum throughput at 550 feet per minute is 275 packages per minute. Reducing the gap increases throughput, but requires more operating precision. A 1″ reduction in the gap means that each package occupies only 23″, and increases throughput to 287 packages per minute. Taking the gap to 8″ increases throughput to 330 packages per minute. The additional 55 packages per minute adds almost 80,000 packages in 24 hours of operation.
Lost Efficiency
Accuracy matters. A loss of just 5% of production, in this case, reduces throughput to 261 packages per minute. Assuming a 24-hour operation, the loss is almost 20,000 packages per day. Put a dollar value on that and it’s easy to see the importance of precision. The conveyor merge, the scanner and the sorter all have to operate at peak efficiency.
Production losses come from several different inefficiencies. At the conveyor merge, the different lanes must be staged so the gap between packages is correct. Too large a gap means that there is too much vacant space on the conveyor. If the desired gap is 12″, but the actual gap is 14″, the maximum production rate becomes 254 packages per minute. The loss is 7.6%.
At 550 feet per minutes, the conveyor travels 2 inches in less than 0.2 seconds, so you can see how easily the proper gapping can be lost.
Conveyor merge errors often result in jams where packages crash together and block traffic. Clearing the jam takes time and costs production.
Misreads at the scanner also affect production. Each misread package costs time, whether because the package recirculates or requires action by an operator.
Bottom Line
Successful high-speed sortation requires excellence in design, installation, programming, and operations. You should be sure to select the right team for the mechanical and conveyor integration, the controls system integration, the installation (both mechanical and electrical), and for your operations. Done poorly, you get headaches. Done well, your investment earns a handsome reward.