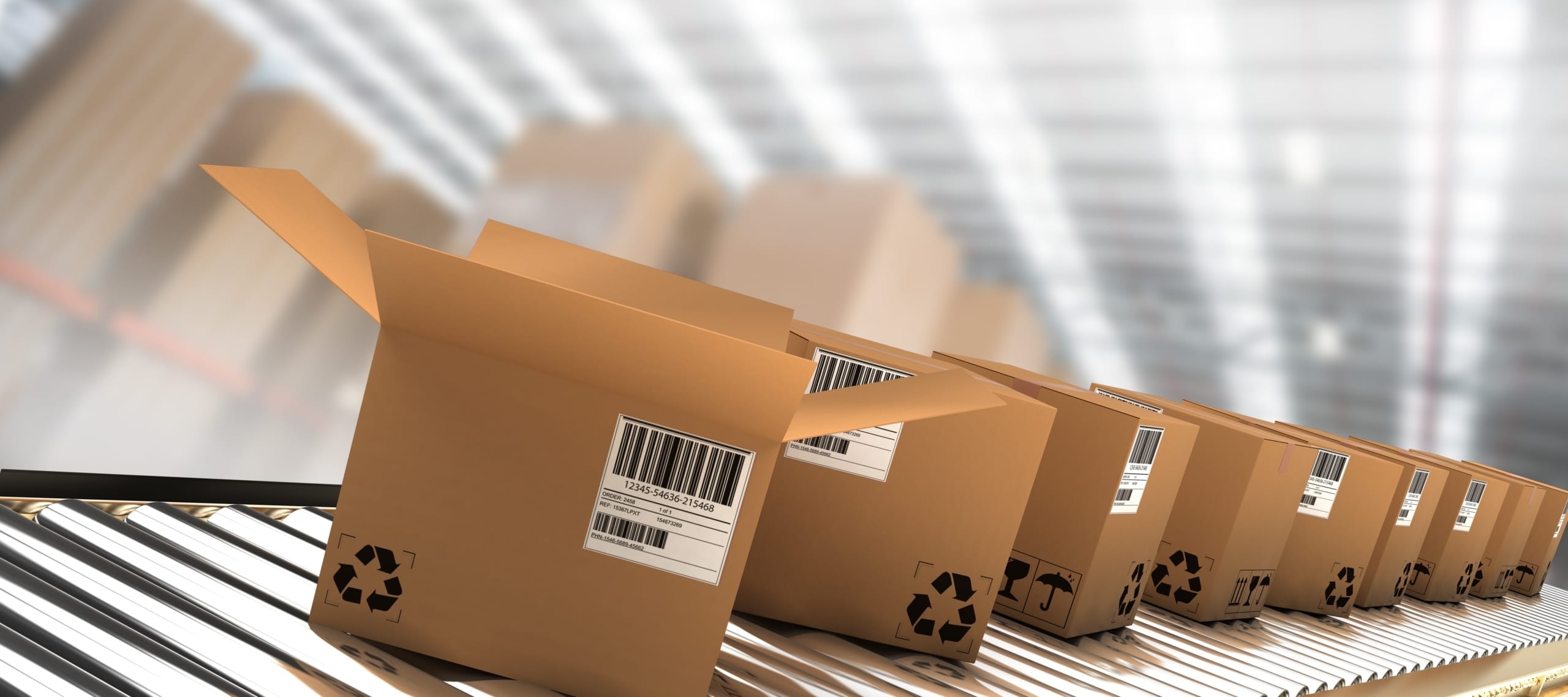
Conveyor Controls – How It’s Done
You get to the startup phase of your project, and now you’re leaning heavily on the conveyor controls to make it all work. Done well, startup goes quickly and the system works. Done poorly, and your well-executed conveyor handling system design and installation seem not to matter because the system isn’t delivering what you promised.
Pendant team members understand the responsibility clearly. We occupy a role that bears similarities to the role of the “closer” in baseball, the pitcher whose job it is to get the final few outs of the game when his team has the lead. In a sense, he can’t win the game, he can only blow it if he does his job poorly. The best closers in baseball readily accept this reality and want the ball in that situation.
Pendant “wants the ball” too. We take great satisfaction from producing systems that work the way they should when they should.
Conveyor Controls Process
Making it all work takes a disciplined process. Here’s the executive summary of how it goes:
-
Preparing your quote
- Our team receives the information you provide, which hopefully includes a CAD drawing of the layout, a conveyor and motor list, a summary description of operations, and information about the totes or cartons and labels.
- We schedule a web conference with your team to have you walk us through the project.
- One of our startup engineers prepares a layout and count, using your CAD drawing, of the control panels and field devices. We either send the field device information to you to give to your electrical installer, or we send it to our electrical installer if you want us to manage the entire process.
- Our estimating team uses the information and our estimating system to produce a fixed price plan to complete the project. Your proposal includes a comprehensive list of all the panels and field devices. It also includes the specifics of the design, programming, startup, and G0-Live engineering services.
-
Executing the Project
- The project management team kicks off the process by creating the electronic project folders and the project schedule.
- The team first engages at what we call the 3PB, which stands for Pendant Project Pre-briefing. In this meeting, the project estimator first reviews the project with the design, programming, and panel assembly team members. We conduct a “pre-mortem” to identify the potential trouble areas. The team “fast-forwards” and imagines that the project has gone poorly and what may have caused that to happen. The team also begins to develop the I/O list.
- The design team produces the drawing sets, including one-line drawings for permitting, control panel drawings, and coordination drawings. Design also produces the full bill of materials (BOM) and orders the parts. In parallel, the programming team writes the preliminary description of operations.
- Once the BOM is ready, the design and panel build teams have a “handoff” meeting. This meeting is used to collaborate and identify the most efficient way to use the available space to create panels that are simple for the operators and maintenance people to understand and use.
- The programming team produces the PLC program that functions as the brains of the system. The programming team also produces a startup and commissioning plan to guide the on-site activities.
- If there is middleware or a Revolution Street WCS included in the project scope, Pendant’s software team creates the appropriate software.
- The panel build team receives the materials and produces the control panels with all labels and tags. The panel build team also assembles the field parts and spare parts, and prepares the shipping crates.
- Once the panels are ready, the programmers test the panels with the program they created.
- Throughout the entire process, there are multiple internal reviews of the drawings, the program, and the panels to ensure quality.
-
After the Panels are Finished
- The panel build team carefully prepares the panels for shipping, and when the time is right, Pendant loads the panels and crates of field parts into a dedicated trailer for transport to the project site.
- Once on-site, Pendant engineers start up and commission the system, and in many cases train the operators and provide Go-Live support.
- The last step, after the project is up and running successfully, led by Project Management, is the 3PD, the Pendant Post Project Debriefing. This meeting is used to review what we learned, what went well, and what we would like to change for future projects.
That’s the conveyor controls process, distilled to fit neatly in a blog post. It may look easy on paper, and we intend to make it look easy in practice. If it does look easy, then we did our job very well.